Toulouse Tech Transfer
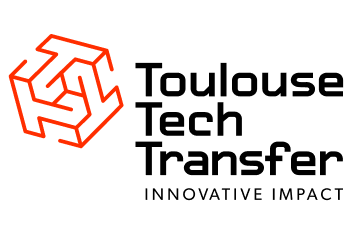
2023 Une année de records
Meilleure année depuis la création de la structure en 2012, l’activité de 2023 confirme la maturité du dispositif et le rôle moteur de la SATT dans le développement d’innovations de rupture (Deeptech) et la création de startups.
À la une
La SATT Toulouse Tech Transfer, c’est :
207
licences
signées
397
brevets
déposés
46
startups
crées et accompagnées
59
millions
d'investissement
Notre SATT Toulouse Tech Transfer vous accompagne pour donner de l’impact à vos projets
À Toulouse Tech Transfer, l'innovation est notre moteur.
Acteurs clés du secteur depuis plus de 10 ans, nos experts détectent auprès des chercheurs les inventions qui auront un impact sur le monde de demain.
L’ambition de notre SATT ?
Contribuer à développer des technologies d'avenir en Occitanie ouest pour une société plus durable et favoriser la création d'emplois comme la compétitivité industrielle. Connecteur privilégié entre chercheurs et entreprises, nous transformons les découvertes de la recherche publique en moteurs d'entreprise et nous soutenons la création de startups deeptech.
Découvrez notre portefeuille
Ingénierie durable & numérique
Life Tech
TTT vous accompagne à chaque étape de votre parcours vers l'innovation
Parce que les experts de notre SATT savent combien la recherche peut être accélérateur d’innovation pour les entreprises et les startups, ils vous proposent un accompagnement complet en valorisation de la recherche.